Barcode Inventory Management System
Barcode Inventory Management System
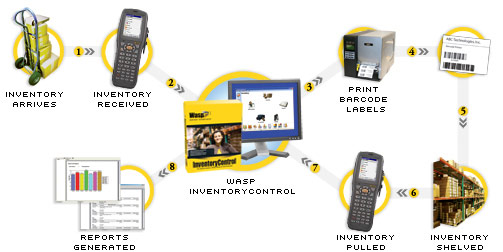
Barcode Inventory systems often utilize Auto ID Data Capture (AIDC) technology, such as barcode scanners, mobile computers, wireless LANs and potentially Radio-frequency identification (RFID) to efficiently monitor the flow of products. Once data has been collected, there is either batch synchronization with, or a real-time wireless transmission to a central database. The database can then provide useful reports about the status of goods in the warehouse. Warehouse Management monitors the progress of products through the warehouse. It involves the physical warehouse infrastructure, tracking systems, and communication between product stations. Warehouse management deals with receipt, storage and movement of goods, normally finished goods, to intermediate storage locations or to final customer.
Key Features Client-server based inventory management software with Barcode enabled data capturing system. Complete visibility to management (from HO) on the inventory at factory as well as depot. Help the management for Production planning with inventory level at factory & Depot. Online Production Report with batch wise. FIFO for Dispatch. 100% accurate automatic data capturing facility in the dusty environment inside the factory. Eliminates any change of manipulations thus gives an accurate report online.
Advatages
• Major Benefits of Automation in Warehouse
• Accuracy of data input (error free)
• Aid effective management of resources and inventories
• Real time data collection
• Measurement of work in progress throughout the factory
• Rapid access to total production costs
• More accurate dispatch
• Accurate and efficient in data reading
• No queuing even during peak time
• No need of experienced hands to operate the machine.
Problem of existing system
Manual Errors: manually-driven procedures in the warehouse cause a number of higher level operational issues in the warehouse (like Inventory may show in stock when in actuality there is an out-of-stock condition, and vice versa.)
Wrong identification of the items: Labels on shipments may be damaged or illegible, causing a long delay in processing, and resulting in congestion at the receiving dock or wrong dispatch/receipt.
Poor utilization of costly warehouse space.
Poor inventory visibility and accuracy which results into erroneous out-of-stock conditions and lost sales.
Manual Product counts results into higher labor costs.
Locating the items: improper sorting, which results in the misplacement of materials on the warehouse shelves & also time consuming.
Reduced Customer Satisfaction: Mis-ships and other shipment delays that ultimately impact customer service satisfaction and retention.
Easy Warehouse Activity
Receiving
Cross docking
Putaway
Inventory control and stock location management
Picking
Sortation and conveying
Shipping
Asset management
Physical control and security
- January 01, 2014Launched New Student Campus Attendance and Student Bus Attendance system
- March 01, 2014Launched New Smart Vehcile Tracking Soluntion
- June 01, 2014Launched New Point of sale and Library Management RFID based solution.